Aerospace Titanium Alloy
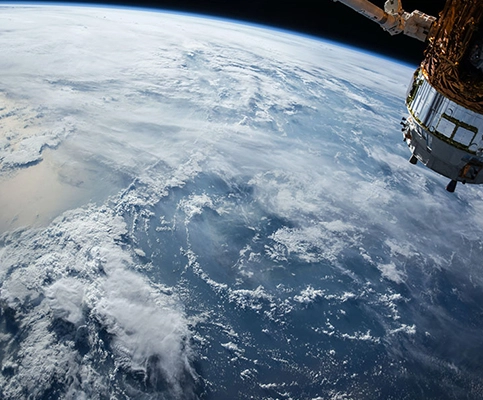
Titanium has many unique properties that make it the ideal choice for various applications in the aerospace industry. Such properties include its high strength-to-weight ratio, excellent resistance to corrosion, and excellent performance at both high and low temperatures. Let Yeshengti titanium factory make list for you, The following are some of the significant uses of titanium in the aerospace industry:
How aerospace titanium alloys used in aircraft?
Since titanium is lightweight and has high strength, it is suitable for use in the production of different parts of an aircraft. These include engine rings, fasteners, wing skins, landing gear, and other structural components.
Aerospace Titanium Alloys for Engine components
The high strength and heat resistance of titanium make it an ideal material for the production of blades, rotors, and other components of aircraft engines. Titanium parts are also resistant to corrosion caused by the acidic exhaust gases and moisture of the engine.
Aerospace Titanium Alloys for fasteners
Titanium is a widely used material for manufacturing bolts, screws, and other fasteners in the aerospace industry. The high strength and corrosion resistance of this metal make it an ideal choice for fasteners necessary in harsh environments, such as the aerospace industry.
Aerospace Titanium Alloys for Heat Shields
Since titanium has exceptional performance at high temperatures, it is suitable for use in heat shields that protect the critical parts of an aircraft. The heat shield of a spacecraft is an excellent example, where it helps to minimize the transfer of heat from the engine to the rest of the spacecraft.
Advantages of aerospace titanium alloys
a. High Strength-to-Weight Ratio
One of the most significant advantages of aerospace titanium alloys is their exceptional strength-to-weight ratio. Titanium is as strong as many steels but has only 60% of the density. This property allows for the construction of lightweight yet sturdy aircraft components, which is crucial for enhancing fuel efficiency and overall performance.
b. Corrosion Resistance
Aerospace titanium alloys possess outstanding corrosion resistance. This resistance to environmental factors, such as moisture and salt in the air, ensures the longevity and reliability of aircraft components. Corrosion-resistant materials are particularly vital for aircraft, which are often exposed to various weather conditions.
c. High-Temperature Performance
Titanium alloys retain their mechanical properties at high temperatures, which is essential for components operating within the extreme heat generated by aircraft engines. The ability to withstand elevated temperatures without significant degradation ensures the safety and performance of these critical parts.
d. Fatigue Resistance
Titanium alloys are known for their resistance to fatigue, which is the weakening of materials under cyclic loading. This property is crucial for components like landing gear that experience repetitive stress during each flight. The fatigue resistance of titanium contributes to the overall safety and lifespan of aircraft.
e. Biocompatibility
While not directly related to aircraft, the biocompatibility of titanium is worth mentioning. It is a non-toxic and biologically inert material, making it suitable for medical implants. Many aircraft components are produced as a result of the aerospace industry's research and development, benefiting from the biocompatibility of titanium.
Which grade of titanium is used in aircraft?
In the aerospace industry, several grades of titanium are used depending on the specific requirements of the component or structure of custom titanium products. The two most commonly used grades are:
a. Grade 5 (Ti-6Al-4V)
Grade 5 titanium, also known as Ti-6Al-4V, is the most widely used titanium alloy in aviation. It consists of 90% titanium, 6% aluminum, and 4% vanadium. This alloy offers an excellent combination of high strength, corrosion resistance, and heat resistance. GR5 titanium plate is commonly employed in aircraft structural components, engine parts, and fasteners due to its remarkable properties.
b. Grade 2 (Ti-CP)
Grade 2 titanium, or Ti-CP (Commercially Pure), is a pure form of titanium with a minimal content of alloying elements. It is highly regarded for its exceptional corrosion resistance, making it an ideal choice for components exposed to aggressive environments. Grade 2 titanium,such as GR2 titanium plate is often used in aircraft where corrosion is a significant concern, such as for fasteners, landing gear, and exhaust systems.
In conclusion, titanium has unique properties that make it ideal for various aerospace applications. With its excellent strength-to-weight ratio, high resistance to corrosion, and heat-resistant properties, it is no wonder that titanium is the preferred choice of many engineers in the aerospace industry. As space travel continues to advance, there will be increased demand to utilize titanium and other advanced materials in space travel and exploration.
Titanium alloys used in aerospace
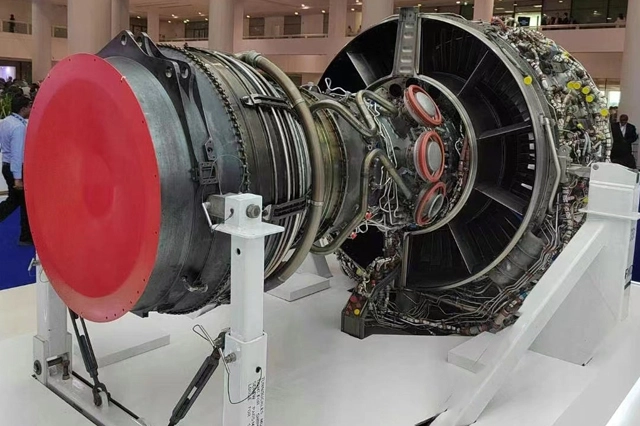
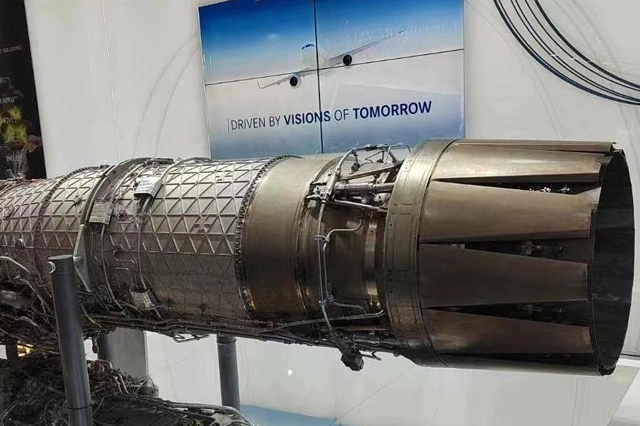
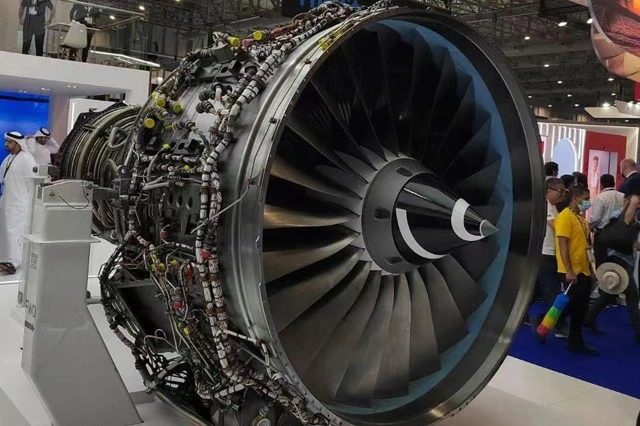